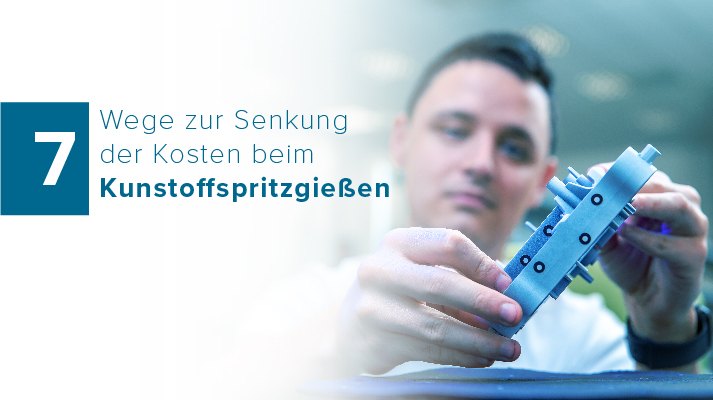
Spritzgießen ist ein kostengünstiger Weg zum Produzieren von Teilen, der jedoch oft mit einer beträchtlichen Abfallmenge verbunden ist, die von Unzulänglichkeiten durch Anwendungsfehler, Maschinenschaden und Stillstandszeiten, hohen Ausschussraten und noch mehr herrührt. Wir stellen Ihnen hier 7 Wege zur Senkung ihrer Spritzgießkosten vor, damit Sie ihr Endergebnis verbessern können.
1. Reduzierung von Risiko und Qualitätskosten
Bei der Reduzierung von Risiko und Qualitätskosten ist häufig ein reaktives Vorgehen statt einem proaktiven Eingreifen festzustellen. Dies liegt daran, dass die Entwicklung von Spritzgussprozessen aufgrund vieler Variablen schwer vorherzusagen ist. Dies setzt uns einem ungeplanten Risiko und Kosten durch die Auslieferung von nicht akzeptablen Teilen aus.
Hier gibt es einen besseren Weg. Beginnen Sie mit dem Einsatz wissenschaftlicher Spritzgießgrundsätze zur Entwicklung eines wiederholbaren, robusten Prozesses. Nachdem der Prozess unter Einsatz von Sensoren und Technologie entwickelt wurde, können Sie ihn auf eine Vielzahl von im Spritzguss üblichen Fehlern überwachen, um eine 100%ige Qualität für ihre Kunden sicher zu stellen.
Wie oft bot sich uns schon dieses Szenario: eine Spritzgießmaschine ist über Wochen im Einsatz und die Prozesstechniker nehmen ständig Anpassungen vor. Die Qualitätsüberwachung warnt uns vor einem Defekt an dem Formteil, so dass wir gezwungen sind, den Prozess zum Beseitigen des Defekts erneut anzupassen, das fehlerverdächtige Produkt zu isolieren und die defekten Komponenten entweder auszusortieren oder nachzubessern.
Im schlimmsten Fall haben wir die Komponenten an den Kunden geliefert und müssen ihn vor dem Problem warnen. Dies ist eine kostspielige Situation. Dadurch, dass kein robuster Prozess auf der Grundlage wissenschaftlicher Spritzgießprinzipien entwickelt und dokumentiert wird, verbringen unsere Techniker ihre wertvolle Zeit mit der Anpassung des Prozesses, um hoffentlich ein Gutteil zu erzeugen.
Nach dem Entdecken des Defekts, werden die Techniker erneut an die Maschine gerufen, um das Problem zu beheben und es besteht die Ungewissheit, ob es nicht wieder auftritt. Jetzt müssen wir uns darüber klar werden, was mit dem Produkt geschehen soll — Aussortieren oder Nachbessern kann sich über Tage oder Wochen hinziehen und ist selten 100%ig effizient. Ganz zu schweigen davon, ist dies eine nicht-wertschöpfende Tätigkeit, da wir Qualität nicht in das Teil hinein prüfen können.
Sind diese Teile zum Kunden gelangt, leidet über kurz oder lang die Geschäftsbeziehung mit dem Kunden. Diese Lage hätte vermieden werden können, wenn wir die Zeit vorab zum Erzeugen und Dokumentieren eines Prozesses aufgewendet hätten, der zur wiederholbaren Produktion hochwertiger Teile geeignet ist. Durch Verwenden von Innendrucksensoren zur Prozessüberwachung lässt sich ein höheres Kontrollniveau einbringen. Stellen Sie sich vor, Sie wissen bereits vor dem Öffnen des Werkzeugs, ob das Teil gut oder schlecht ist und können es automatisch sortieren.
2. Steigerung der Effizienz durch Automatisierung
Mit Hilfe von Technologie und Schulung können Sie verschiedene Produktionsbereiche automatisieren, um so die Effizienz der Arbeitskräfte und der Produktion erhöhen. Teileentnahme, Stapelung und Palettierung von Teilen sind drei Arten der nützlichen Automatisierung. Die Prozesssteuerungstechnologie kann die automatisierte Teilesortierung und Warnungen ermöglichen, die ihnen melden, wenn ein Prozess außerhalb der Toleranz liegt. So wird die Effizienz und Genauigkeit durch die Bereitstellung von Daten weiter gesteigert, die ihnen eine schnelle Ursachenforschung ermöglicht. Sie können die Fehlersuche einstellen und anfangen, Probleme direkt im Ansatz auszumerzen.
Denken Sie an Prozesse in einer Produktionsanlage ohne Automatisierung. Beim Durchlaufen des Prozesses müssen wir das Teil und das Kanalsystem aus dem Werkzeug heraus nehmen, die Teile für das Verpacken organisieren, das Endprodukt verpacken und dann palettieren. An irgendeiner Stelle im diesem Prozess ergänzen Sie möglicherweise einen Montageschritt, der zusätzliche Arbeitskraft, Platzbedarf und Zeit bedingt.
Beim Ausführen dieser Prozesse von Hand ergibt sich stets ein uneinheitlicher Effizienzgrad im Prozess. Betrachten wir einmal allein die Entnahme der Teile aus dem Werkzeug, so werden selbst die Bediener mit der besten gleichbleibenden Leistung Unterschiede in der Zykluszeit verursachen, was zu Schwankungen der Teilequalität führt. Dies wird dann in jedem Prozessschritt verschlimmert.
Sobald wir anfangen, den Prozess zu automatisieren, beginnen wir Unstimmigkeiten abzustellen, die Effizienz zu steigern, die Qualität zu verbessern und die verfügbare Nutzfläche zu vergrößern. Die Automatisierung der Qualität — sei es durch Prozessüberwachung, Vision Systeme oder Inline-Maßkontrolle — kann sicherstellen, dass unsere Kunden niemals wieder ein defektes Produkt erhalten.
3. Steigerung des Bewusstseins für die Prozessstreuung (Reduzierung von Ausschuss)
Durch die sofortige Kenntnis, wann eine Abweichung in einem Prozess auftritt, können Sie Probleme schneller abstellen. Dies bedeutet weniger Ausschuss, ermöglicht einen höheren Nutzungsgrad der verfügbaren Maschinenlaufzeit und weniger Geld, das im Müll landet. Dies lässt sich für Sie durch Prozesssteuerungssoftware, Werkzeuginnendrucküberwachung und Schulung erzielen.
Die Fertigung enthält stets inhärente Qualitätskosten. Diese Kosten ergeben sich am Ende der Produktion durch Verwenden wertvoller Ressourcen und der Zeit zur Kontrolle der Teile, bevor diese an den Kunden versandt werden können. Das Problem ist, dass wir niemals feste Qualitätskosten erreichen werden. In dem Maß, in dem die Produktion variiert, ändert sich auch die Sortierzeit und die Anzahl an Mitarbeitern, die zum Sortieren des Produkts erforderlich sind.
Ist die Mitarbeiterfluktuation ein Thema, bedarf es einer Investition in die Schulung neuer Mitarbeiter zum Aussortieren defekter Teile. Indem Sie sicherstellen, dass alle Techniker nach dem gleichen Standard geschult werden, können Sie beim Reduzieren oder Abstellen von Ausschussteilen proaktiv eingreifen, statt bei hohen Ausschussraten auf Grund niedriger Qualifikationsniveaus und schlecht eingerichteter Prozesse mit kleinen oder nicht vorhandenen Prozessfenstern reaktiv und nach dem Prinzip der Brandbekämpfung vorzugehen.
Eine weitere Möglichkeit zur Betrachtung der Qualitätskosten ist der Fokus direkt auf den Anfang. Durch das Integrieren der Qualität in einen Prozess und deren Überwachung über den gesamten Zyklus hinweg, können wir erkennen, wann eine Prozessabweichung auftreten kann. Wissen wir beispielsweise, dass bei einem Material eine erhebliche Viskositätsänderung auftritt, die zu Qualitätsproblemen führt, können wir Prozessüberwachungswerkzeuge zum Erkennen einer Viskositätsänderung einsetzen. An diesem Punkt kann der Prozess neu zentriert werden, um wieder Qualitätskomponenten zu produzieren.
4. Einkauf von Rohmaterial nach breitem Anforderungsspektrum
Rohmaterial mit einer großen Spannbreite an Eigenschaften ist günstiger, doch kann die Überprüfung oder Beibehaltung der Maße bei Teilen mit engen Toleranzen schwieriger sein. Dies kann die Variabilität und damit die Ausschussraten erhöhen, doch wenn wir DECOUPLED MOLDING® Techniken in Verbindung mit Werkzeuginnendrucksensoren einsetzen, kann dies ein erfolgreiches Vorgehen sein.
Wie oft standen Sie bereits diesem Szenario gegenüber: über Tage hinweg produzieren Sie gute Teile und dann, aus heiterem Himmel, bemerken Sie auf einmal immer mehr Teile mit Grat. Zum Abstellen dieses Problems setzt der Prozesstechniker die Füllgeschwindigkeit herab. Wenige Stunden später wendet sich die Qualitätsabteilung wegen unvollständiger Füllungen an Sie. Warum kam es nach der Produktion der guten Teile urplötzlich zu dieser Gratbildung? Die Antwort darauf liefert höchst wahrscheinlich die Viskosität.
Viskosität kann oftmals um 30 % in jede Richtung schwanken, wodurch die Herstellung eines guten Teils selbst bei einem Decoupled II-Prozess sehr schwierig wird. Um sicherzustellen, dass in jedem Zyklus (oder zumindest so oft wie möglich) die gleichen Teile hergestellt werden, ist der Einsatz von Werkzeuginnendrucksensoren zur Prozesssteuerung und zum Minimieren der Viskoseänderungen im Material erforderlich.
5. Niedrige Zykluszeit
Sie können wissenschaftliche Spritzgieß- und DECOUPLED MOLDING® Techniken einsetzen, um Schließ-/Auswerfbewegungen, Einspritzzeit, Vierdichtungszeit, Nachdruckzeit und Kühlung zu optimieren. Dabei entscheiden Sie, was genau notwendig ist, um Gutteile mit einem kleinen Puffer herzustellen.
Richtig dimensionierte Werkzeugtemperaturreglereinheiten, Thermolatoren, helfen ebenfalls bei der Reduzierung der Zykluszeiten. 80 % der Spritzgießzykluszeit wird für die Kühlung des Teils von der Schmelzetemperatur auf eine Auswurftemperatur aufgewendet, bei der das Teil fest genug ist, um den Auswurfkräften zu widerstehen und die Maßhaltigkeit zu behalten. Bei einem unzureichenden Wasserfluss ist die Fähigkeit zur Kühlung des Teils auf die korrekte Temperatur beeinträchtigt und als Behelfslösung wird das Teil länger im Werkzeug belassen, was höhere Kosten verursacht.
Die Bewertung der Teiledicke zu Projektbeginn ist der erste Schritt zur Bestimmung der Zykluszeit. Unbedingt zu klären ist die Frage nach der Dicke des Teils und wie sich diese auf die Zykluszeit und das Leistungsverhalten des Teils auswirkt. Häufig stellen wir fest, dass Teile in einer bestimmten Art und Weise konstruiert sind, „weil wir dies schon immer so gemacht haben“. Wie Sie sich vorstellen können, kann dies sehr kostspielig sein. Wissenschaft und Simulation helfen bei der Vorhersage des Erfolgs der Konstruktion, wodurch Bau und Erprobung für das Erzielen von Ergebnissen nicht mehr erforderlich sind. Die Sicherstellung der richtigen Teilekonstruktion ist nur ein Beispiel dafür, wie Sie ihre Gesamtzykluszeit reduzieren können.
6. Bau effizienterer Werkzeuge
Einfach ausgedrückt ist ein Werkzeug ein Druckbehälter und ein Wärmetauscher — in der Kavität wird stets ein Druckverlust auftreten. In den meisten Fällen gilt: je geringer der Druckverlust von Angussnähe zu Kavitätsende, desto weniger wahrscheinlich werden Qualitätsprobleme wie Verzug, Lunker, Einfallstellen, unvollständige Füllungen oder Maßabweichung sein.
Damit das Rohmaterial fließt, müssen wir es erwärmen, doch zum Auswerfen müssen wir einen Teil der Wärme entfernen. Für den Bau eines effektiven Werkzeugs ist es entscheidend, sicherzustellen, dass die Wasserleitungen richtig platziert sind. Wir müssen außerdem ein Metall wählen, das Wärme überträgt, dem Material jedoch auch widerstehen kann (insbesondere einem Material mit Glas- oder Carbonfaserfüllstoff). Schließlich muss der Prozess mit einem kraftvollem Wasserfluss eingerichtet werden, damit gewährleistet ist, dass das Werkzeug rasch die thermische Stabilität erreichen und über einen langen Produktionslauf hinweg beibehalten kann.
Sie können die Effizienz des Werkzeugs auch durch Vergrößern der Kavität verbessern. Ein-Kavitäten-Werkzeuge bieten die geringste Variabilität, jedoch ist der Preis zur Herstellung jedes einzelnen Teils nacheinander extrem hoch. Sind mehrere Kavitäten möglich, können Sie mehr Teile in derselben Zeit herstellen. Die Anzahl der möglichen Kavitäten unterliegt Beschränkungen, zu denen Vorgaben an Qualität, Werkzeug- und Maschinenabstand und die Überprüfung gehören.
Ein weiterer Weg zur Steigerung der Werkzeugeffizienz stellt der Bau von Familienwerkzeugen dar, die unterschiedliche Teilegeometrien im selben Werkzeug enthalten. Dies kann sich als extrem schwierig erweisen, da die vier Massevariablen in jeder Kavität unterschiedlich sind. Mit Prozesssteuerungssoftware und Werkzeuginnendrucksensoren können Sie allerdings die Verschlussdüsen zur separaten Kontrolle jeder Kavität einsetzen.
7. Verringerung der Werkzeugtransferkosten
Prozessentwicklungsanwendungen stellen sicher, dass Sie ein Werkzeug rasch und mühelos von einer Maschine auf eine andere übertragen können. Maschinenspezifische Einrichtblätter werden beim Transfer des Werkzeugs automatisch erzeugt, so dass Sie Gutteile ab dem ersten Einspritzen herstellen können. Diese Kurven können in jeder Maschine verwendet werden, so lange diese in der Lage ist, für eine angemessene Fließgeschwindigkeit, Drücke, Temperaturen und Volumen zu sorgen. Falls keine Simulation verwendet wird, können wir auch Referenzkurven erzeugen und diese an jede leistungsfähige Maschine übertragen.
Sparen Sie Zeit, Energie und Ressourcen, indem nicht Sie ihre eigenen ungeregelten Umwandlungswerkzeuge erschaffen müssen oder den Prozess für jede neue Maschine von Grund auf neu aufbauen müssen.