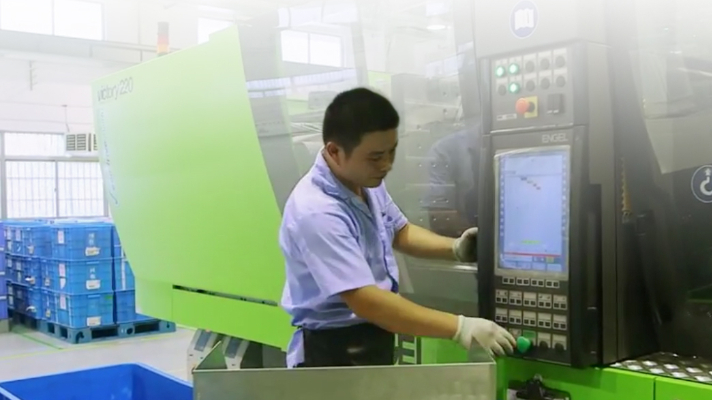
The Challenge
We run between 250,000 and 300,000 mirrors a week. That equates to extremely fast cycle times for parts that are shipped all over the world. If we have a quality spill it isn’t uncommon for it to hit three continents, so it’s really important that we make a good part every time.
To add to our challenge, we have an extremely intricate design on our tools. There’s an undercut in the mirror case that holds the glass from going forward, and the case shrinks around the glass. That undercut is so severe that we have to run with a bunch of lifters that form it. Those lifters are so precise that they have a one and a half thousandth interference fit to each other and to the steel.
One of our challenges was that we were doing a lot of damage to our tools due to breaking those lifters. In addition to the broken mold components, we also struggled with short shots, size variation, and downtime.
The Solution
We tried many tools in the past, including process log books and training, but nothing we used was able to completely resolve our issue. Since my previous experience with RJG was positive, we decided to implement the eDART SystemTM and cavity pressure sensors on all of our machines. I’ve been working with RJG for 15 years now and can’t imagine running a machine without it.
The Result
RJG has allowed us to stop breaking lifters and sending bad parts across the world. We no longer make bad parts, but if one does happen to sneak through, we’re able to contain it quickly and prevent it from being shipped to the customer. We used to work on at least one mold every month for lifter damage. Since implementing RJG, we’ve gone over a year without damaging a single lifter.
RJG improved our quality and the robustness of our tools. We’re now able to sort, contain, eliminate mold damage, and minimize scrap. That cost savings allowed us to get a third press in the shop, which also has RJG on it. After as much as we’ve saved with RJG’s equipment, it’s too expensive not to use. We’ll never have a machine without RJG equipment installed again.
Tim Cleveland
Molding / Tooling Engineer
Magna Mirrors of America
About Magna
We are a leading global automotive supplier with 312 manufacturing operations and 98 product development, engineering, and sales centres in 29 countries. We have over 155,000 employees focused on delivering superior value to our customers through innovative processes and World Class Manufacturing.